In today’s rapidly evolving industrial landscape, where competition is fierce and efficiency is paramount, the integration of human resources and digitalization has emerged as a powerful catalyst for improving performance in factories. As factories adopt advanced technologies and automation, harnessing the full potential of their workforce becomes crucial. By leveraging the power of digital tools and optimizing human resource management practices, industrial factories can unlock new levels of productivity, enhance employee engagement, and drive sustainable growth.
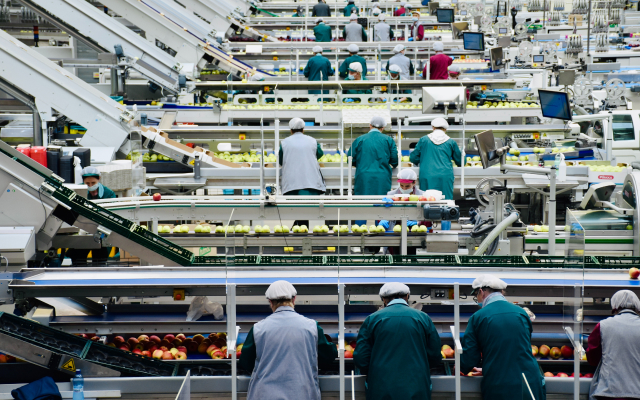
Top 5 benefits of unleashing the performance potential in Industry through Human Resources
1. Enhanced Workforce Planning and Talent Acquisition
Digitalization enables industrial factories to streamline their workforce planning and talent acquisition processes. Through advanced data analytics, factories can identify skill gaps, assess the future demand for talent, and proactively plan their recruitment strategies. By leveraging artificial intelligence (AI)-powered algorithms, HR departments can effectively match job requirements with candidate profiles, leading to improved talent acquisition and reduced hiring time.
2. Upskilling and training
With the rapid advancement of technology, it is essential for industrial workers to continually update their skills. Digitalization plays a pivotal role in facilitating upskilling and training programs. E-learning platforms, virtual reality (VR) simulations, and augmented reality (AR) tools can provide immersive and interactive training experiences, enabling employees to acquire new competencies and adapt to evolving job roles. By investing in continuous learning, industrial factories empower their workforce to embrace technological advancements and contribute to organizational success.
3. Smart workforce management
Digital tools and platforms offer robust solutions for effective workforce management. Automated scheduling systems can optimize shift planning, taking into account factors such as employee preferences, skills, and workload requirements. These tools help minimize errors, reduce downtime, and ensure an optimal balance between employee well-being and operational needs. Additionally, digital HR platforms provide real-time performance monitoring, enabling managers to track employee productivity, identify bottlenecks, and provide timely feedback for improvement.
4. Collaborative communication and employee engagement
Digitalization provides numerous communication channels that foster collaboration and enhance employee engagement within industrial factories. Instant messaging platforms, project management tools, and video conferencing solutions enable seamless communication and knowledge sharing across teams and departments. Employees can collaborate in real-time, share best practices, and contribute to problem-solving, leading to increased efficiency, innovation, and overall job satisfaction.
5. Predictive analytics for performance optimization
By leveraging advanced analytics and predictive modeling, industrial factories can optimize performance and operational efficiency. HR departments can analyze historical data, identify patterns, and predict future trends related to workforce performance, absenteeism, and turnover rates. This enables proactive interventions, such as personalized coaching, targeted performance improvement initiatives, and retention strategies. By harnessing the power of data, factories can make informed decisions that maximize productivity and optimize resource allocation.
Conclusion
The convergence of human resources and digitalization is revolutionizing industrial factories, driving performance improvements, and unlocking their full potential. By strategically integrating digital tools into HR practices, factories can enhance workforce planning, optimize talent acquisition, and facilitate continuous upskilling. Smart workforce management solutions enable efficient scheduling and real-time performance monitoring. Collaborative communication channels foster engagement and knowledge sharing. Finally, predictive analytics empowers factories to optimize performance and make data-driven decisions.
As industrial factories embrace digital transformation, they not only enhance productivity but also create a positive work environment that attracts and retains top talent. By recognizing the power of human resources and digitalization, industrial factories can embark on a journey towards sustainable growth, competitive advantage, and success in the digital era.
Share this post