Downtime is one of the most costly and frustrating challenges for any manufacturing plant. It can result from various factors, such as equipment failures, human error, supply chain disruptions, or external events.
Fortunately, there is a way to minimize downtime and optimize plant performance: use data analytics to identify the root causes of downtime, predict and prevent potential problems, and improve your overall efficiency and productivity.
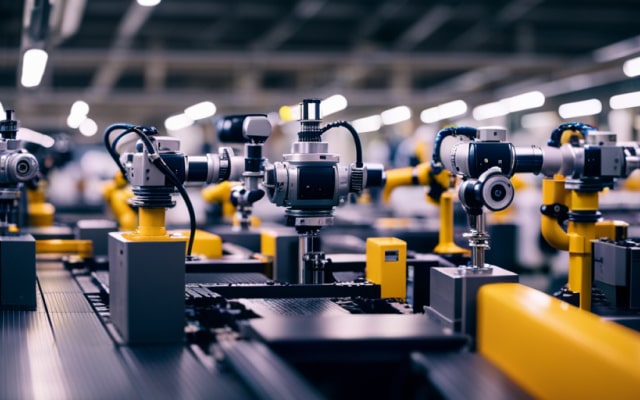
The benefits of data analytics to reduce downtime in your plant
Data analytics can help you reduce downtime in several ways, including:
- Improve quality and accuracy: By analyzing data on product quality, customer specifications, and industry standards, you can detect and correct any defects or deviations before they affect production.
- Increase availability and reliability: By analyzing data on equipment health and performance, you can monitor and maintain your critical assets, prevent unexpected failures, and schedule repairs or replacements in advance.
- Optimize efficiency and productivity: By analyzing data about processes and operations, you can identify and eliminate bottlenecks, waste, and inefficiencies, improve workflow, and increase capacity and speed.
- Improve safety and compliance: By analyzing data on risks and regulations, you can prevent accidents, injuries or fines, ensure a safe environment for your employees and customers, and comply with legal and ethical standards.
The types of data you need to collect and analyze
To get the most out of data analytics, you need to collect and analyze different types of data related to your plant, such as:
- Historical data: is the data you have collected in the past about your production, quality, maintenance, inventory, etc. This data allows you to understand how your plant has performed under different conditions and periods.
- Real-time data: is the data that is continuously generated from sensors, devices or systems that monitor your plant. This data allows you to see what’s happening in your plant right now and react quickly to any issues or opportunities.
- Predictive data: is the data that is derived from statistical analysis or machine learning that allows you to predict what will happen in your plant in the future. This data allows you to anticipate potential problems or improvements and plan ahead.
The tools and techniques you can use for data analysis
To perform effective data analysis, you need to use appropriate tools and techniques that allow you to collect, store, process, visualize, and communicate your findings. Some common tools and techniques are:
- SCADA (Supervisory Control and Data Acquisition) systems: these are systems that allow you to control and supervise your industrial processes through a graphical interface. They also allow you to collect and store large amounts of real-time data from different sources.
- IoT (Internet of Things) platforms: These are platforms that allow you to connect and communicate with smart devices, such as sensors, cameras or robots, that can collect and transmit data about your plant. They also allow you to process and analyze data in the cloud or at the edge (edge computing).
- BI (Business Intelligence) software: these are programs that allow you to visualize and explore your data through dashboards, graphs or reports. They also allow you to perform descriptive, diagnostic, predictive, or prescriptive analytics to gain insights and make decisions.
- ML (Machine Learning) software: These are programs that allow you to apply machine learning algorithms to your data to discover patterns, trends or anomalies. They also allow you to create predictive or prescriptive models that can improve your performance.
Focusing on our RTM Pro application we have several tools available to improve factory performance:
- FlowOrder: tool that allows us to visualize the flow that the products have followed, as well as to visualize the processes that consume the most time and try to reduce these times.
- CTT: tool that calculates the pause times between the products, being able to associate the pause times with changes in the machine that usually produces
- CO Analysis: This tool shows us these machine changes, when they occur, how long they take and how many products have been made until it is changed again.
Best practices for implementing data analytics in your plant
To implement data analytics in your plant successfully, you need to follow some best practices, such as:
- Define your goals and metrics: Before you start collecting and analyzing data, you need to be clear about what you want to achieve and how you will measure it. For example, if you want to reduce downtime, you need to define what downtime means to you, how you’ll calculate it, and what your goal is.
- Choose the right sources and data types: Based on your goals and metrics, you need to select the sources and data types that will provide you with the most relevant and accurate information. For example, if you want to predict downtime, you need to collect data on equipment health and performance, as well as environmental or market conditions.
- Ensure data quality and security: To make sure your data is reliable and useful, you need to verify its accuracy, integrity, consistency, and up-to-dateness. You also need to protect your data from unauthorized access, loss or damage.
- Use the right tools and techniques: Depending on your needs and capabilities, you need to choose the tools and techniques that allow you to collect, store, process, visualize and communicate your data efficiently and effectively. You also need to train your staff so they can use them correctly.
- Monitor and continuously improve: Once you have implemented data analytics in your plant, you need to monitor your results and compare them to your goals and metrics. You also need to evaluate the impact of your actions and look for ways to improve your process and performance.
Conclusion
Data analytics is a powerful tool that can help you reduce downtime in your plant. By using data analytics, you can improve quality and accuracy, increase availability and reliability, optimize efficiency and productivity, and improve security and compliance. To get the most out of data analytics, you need to define your goals and metrics, choose the right data sources and types, ensure data quality and security, use the right tools and techniques, and continuously monitor and improve.
If you’d like to learn more about how you can use data analytics to reduce downtime in your plant, contact us today. We can help you implement a custom solution that fits your specific needs.
Share this post