Digital twins have emerged as a technology that is reconfiguring the industrial and process sector. This technology creates virtual replicas of physical assets, processes or complex systems.
In this article we will delve into the field of digital twins, describing the current landscape, defining it, detailing its benefits, challenges and important data.
Introduction to Digital Twins
A digital twin is a virtual representation of a physical object, process or system. In other words, when we talk about this concept, we are referring to a kind of digital clone that focuses on copying the characteristics and behavior of its real counterpart.
This replica is fed by data that constantly emerges from sensors and other devices connected to the physical object. Through them, monitoring, analysis and simulation are possible.
How digital twins work
Data Collection and Integration
Sensors are used to obtain real-time data from physical objects. These physical devices can be IoT devices, sensors, or other sources to create a real-world picture of the object or system. This generated data includes information about its status, performance, and so on.
Modeling and Simulation
From the data that is collected, a three-dimensional model is created that includes all the important data: dimensions, materials, components… In other words, simulations are created to provide information, solve problems and make more informed decisions.
Real-Time Monitoring and Analysis
With digital twins, the physical counterpart is continuously monitored, analyzing data to provide insights, troubleshoot problems, and make informed decisions.
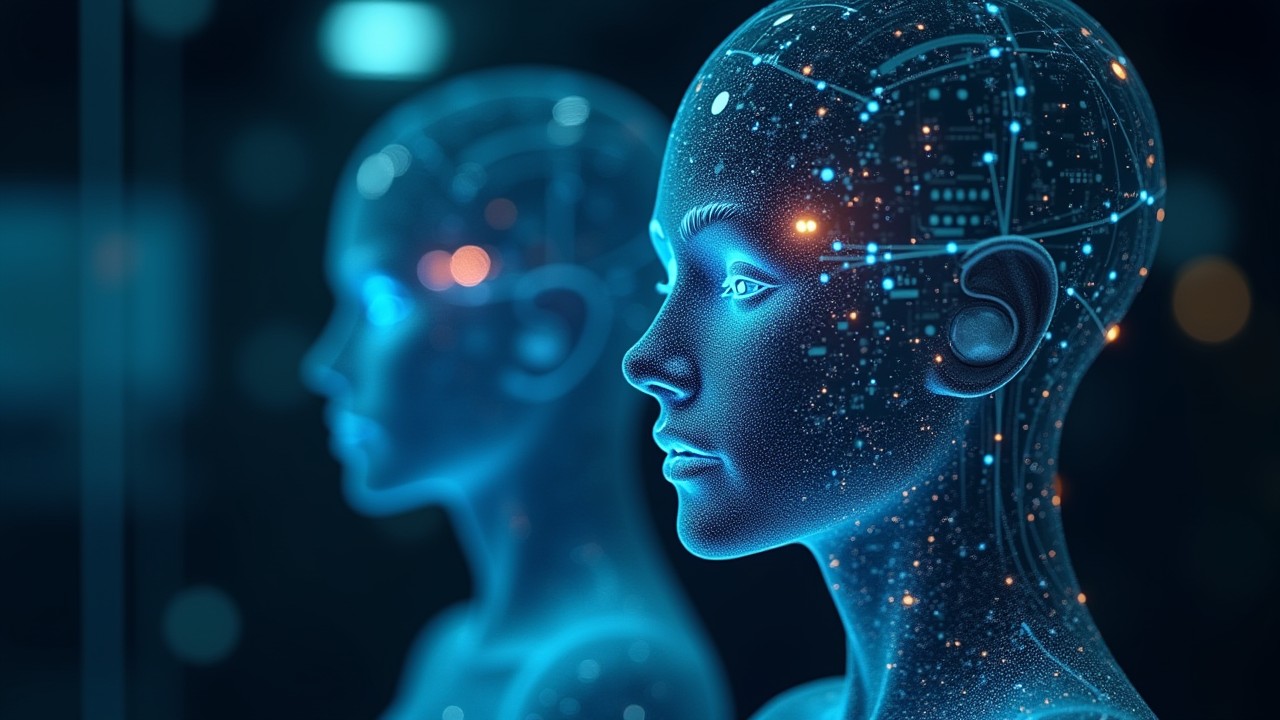
Benefits generated by digital twins
The benefits of digital twins include improved operational efficiency, reduced maintenance costs and the ability to predict failures before they occur.
Optimization of processes and operations
Digital twins offer a powerful tool for optimizing processes and operations across a wide variety of industries. Digital twins provide a holistic, real-time view of physical systems, allowing organizations to identify inefficiencies, predict failures, and optimize operations in unprecedented ways.
Improving decision making
They allow for a deeper visualization and understanding; by creating a digital replica, a clearer and more detailed view of a system or process is obtained. In addition, it allows for simulating different scenarios, generating predictions and preventing the future behavior of a system, reducing costs…
Innovation and product development
It facilitates the creation of new products and services more quickly and efficiently, allowing experimentation with different designs and configurations without the need to invest in physical prototypes. It is also capable of potentially reducing the time needed to bring a new product or service to market.
Process optimization
It allows you to simulate different scenarios and analyse their impact before implementing them in the real world, reducing risks and costs. Digital twins help to identify and solve efficiency problems in production, logistics and maintenance processes.
Training and coaching
Digital twins can be used to create realistic training simulations, allowing employees to acquire new skills and knowledge safely and efficiently.
But that’s not all, with this system there is continuous improvement, as it facilitates the implementation of improvements and the constant optimisation of processes.
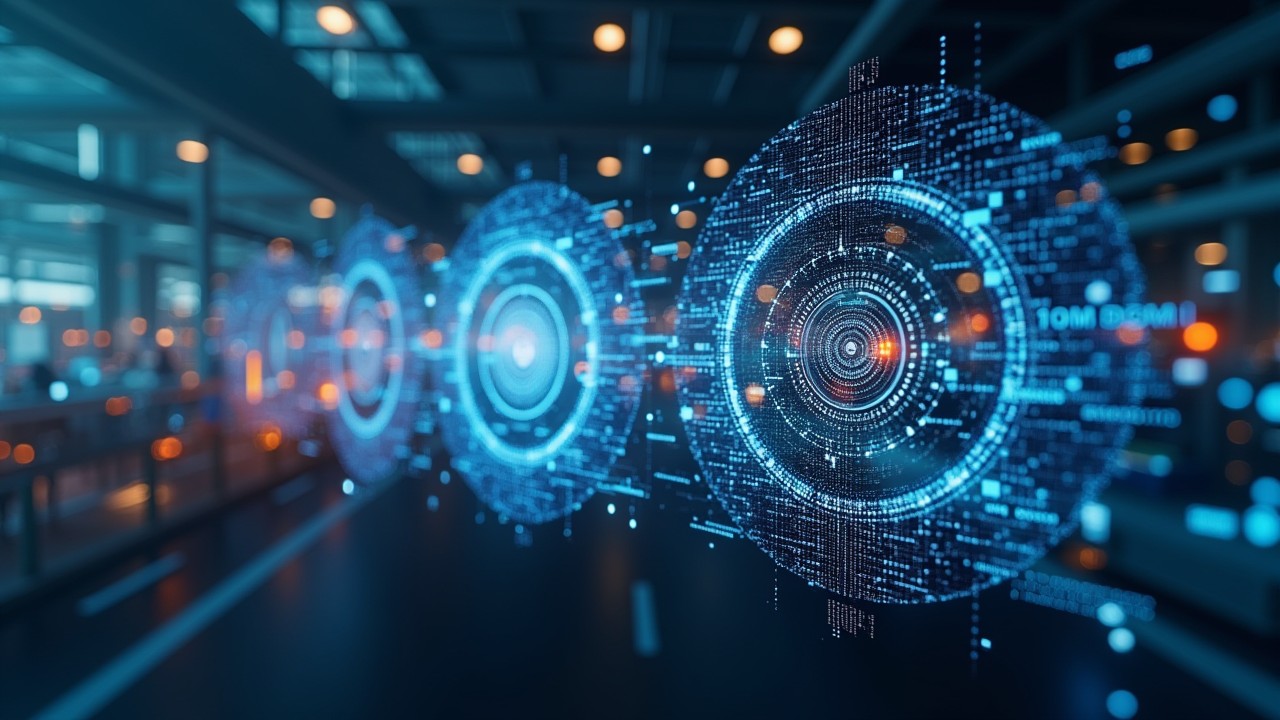
Conclusion
Digital twins are defined as a transformative technology that is redefining the way we manufacture and operate complex systems. By offering an accurate, real-time virtual representation, these models make it possible to optimize processes, anticipate failures, and make more informed decisions.
They also offer a multitude of benefits for various industries, from reducing costs and increasing efficiency to improving product quality and making decisions more agile.
In addition to presenting great potential, their implementation can pose great challenges, but they remain a very powerful tool in the industrial sector.
Share this post