Operational excellence has always been the key objective of industrial companies, but in 2025, this concept will take on a new meaning. Advancing technology and the adoption of data-driven tools are transforming how companies manage their processes and optimise their operations. The key is no longer just to react to problems, but to anticipate them and make data-driven decisions in real time.
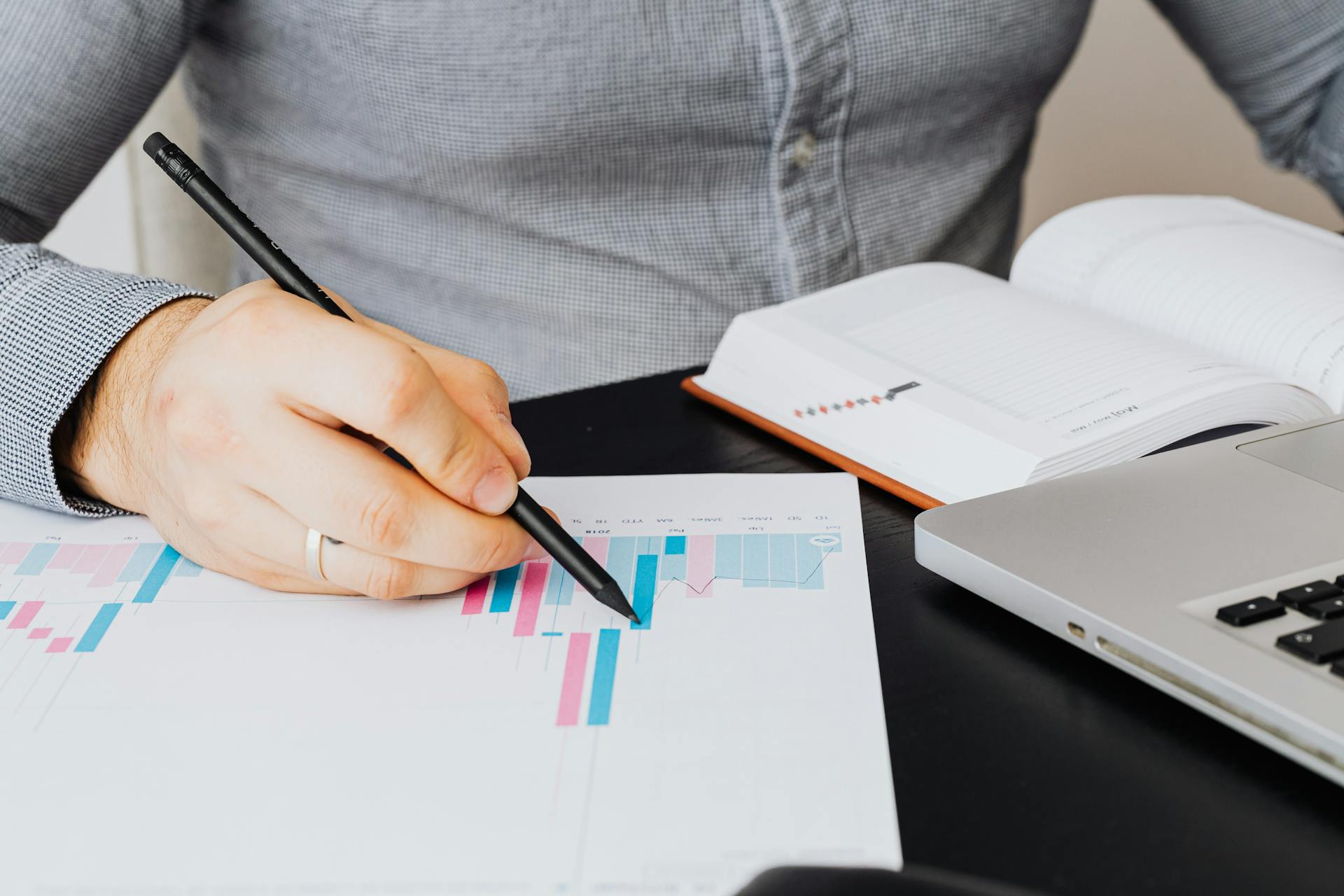
The central role of data in 2025
Organisations generate massive amounts of data in their day-to-day operations, but only those that know how to leverage it will stand out in the marketplace. The companies that lead the change will be the ones that turn that data into concrete actions and tangible results. According to recent studies, 70% of companies believe that real-time analytics will be essential to achieving their strategic goals in the coming years.
At AppliediT, we have helped companies in a variety of industries transform the way they work using technologies such as RTM Pro, our advanced industrial process improvement and analytics solution.
6 pillars for achieving operational excellence by 2025
- Real-time analytics
The ability to monitor and analyse data in real time is essential to detect problems early and avoid costly delays. Tools such as RTM Pro allow you to visualise key metrics in real time, identify bottlenecks and react quickly to any deviations.For example, one automotive manufacturer was able to reduce its cycle times by 15% by immediately identifying inefficiencies on its production line. - Machine learning applied to manufacturing
Machine learning can identify hidden patterns in historical data and predict failures before they occur. This translates into more effective predictive maintenance strategies, less downtime and better use of resources.A typical case is the detection of anomalies in critical machines, which avoids unplanned downtime and ensures that production deadlines are met. - Connectivity through the IIoT
The Industrial Internet of Things (IIoT) allows every machine, sensor and device in the plant to be connected and send data to a centralised platform. This provides a holistic view of operations and allows decisions to be made based on a complete picture.In addition, this connectivity facilitates integration between equipment from different manufacturers, ensuring interoperability and maximising the use of existing assets. - Data-driven optimisation
Operational excellence involves not only solving current problems, but also continuously improving processes. Using real-time and historical data allows you to identify trends, eliminate inefficiencies and optimise key processes to increase productivity.For example, by analysing a full year’s production data, a consumer goods company was able to adjust its assembly lines, increasing throughput by 10% without the need to invest in new machinery. - Integrated quality management
Quality remains a key differentiator, and data can play a key role in managing it. By integrating analytical tools with quality control systems, companies can identify deviations in real time and correct them before they affect the end customer.RTM Pro, for example, can link detected defects to specific process variables, helping to identify root causes and prevent recurrence. - Data-driven decision making
Rather than relying on intuition or individual experience, data can provide an objective basis for making strategic decisions. From fine-tuning production planning to optimising inventory levels, advanced analytics provides the insight needed to minimise risk and maximise results.At AppliediT, we’ve seen how the use of customised dashboards and dynamic reporting makes it easier for plant managers to make decisions aligned with overall business objectives.
Real results
Leading companies that have adopted these practices are already seeing results. From 20% reductions in downtime to significant increases in product quality, data-driven operational excellence is not a future promise – it’s a reality.
If you want to be among the companies leading the change by 2025, now is the time to act. Want to know how RTM Pro can help you transform your operations? Contact us and find out how we take our customers to a new level.
Share this post