Imagine having a mirror image of a physical object or process, but in the digital world. That’s exactly what digital twins are all about! These virtual replicas, using the power of IoT and advanced analytics, are revolutionizing the manufacturing and supply chain industry in ways we couldn’t have imagined.
So, what exactly are digital twins? They are virtual replicas of physical assets, systems, or processes that mimic their real-world counterparts. These twins capture real-time data, providing insights and enabling us to make informed decisions.
In the manufacturing industry, digital twins are bringing a whole new level of efficiency and innovation. Improved product design and development allow companies to identify flaws before they occur in the physical world. Optimized production processes ensure smoother operations and reduced downtime. And with predictive maintenance, equipment failures become a thing of the past.
But it doesn’t stop there! Digital twins are also transforming the supply chain industry. With enhanced inventory management, businesses can optimize their stock levels, reducing wastage and costs. Enhanced logistics and shipping enable streamlined operations, ensuring the right products reach the right place at the right time. And with demand forecasting, companies can cater to customer needs with precision.
Of course, like any technological advancement, digital twins come with their own set of challenges. Privacy and security concerns need to be addressed to protect sensitive data. Integration challenges may arise while connecting various systems and platforms. However, the future potential of digital twins is undeniable. As technology continues to advance, the possibilities for improvement and innovation are limitless.
In a nutshell, digital twins are changing the game in the manufacturing and supply chain industry. With their ability to replicate physical assets and processes in the digital realm, they offer increased efficiency, cost savings, and improved decision-making. Get ready to witness the revolution firsthand!
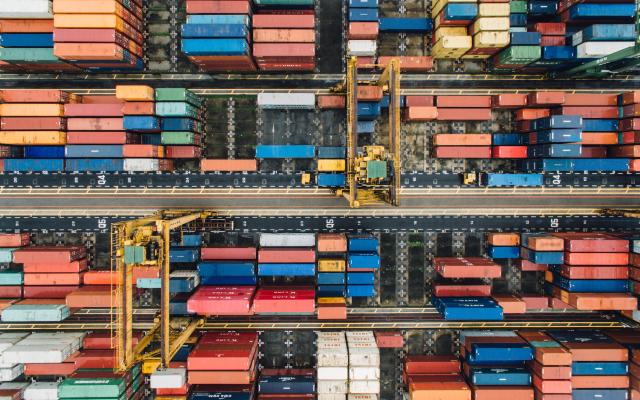
How do Digital Twins work?
Now, let’s dive a bit deeper into the functioning of these digital doppelgangers. Digital Twins work by constantly capturing and monitoring data from their physical counterparts using sensors. This data is then analyzed to provide insights, identify potential issues, and optimize performance. It’s like having a personal trainer for your manufacturing processes or supply chain systems, who constantly guides and assists you in making better decisions.
Revolutionizing the Manufacturing Industry
When it comes to the manufacturing industry, Digital Twins have a profound impact. Improved product design and development is one of the key advantages. Manufacturers can create virtual prototypes, simulate different scenarios, and make necessary adjustments before even producing the physical product.
Optimized production processes are another area where Digital Twins shine. By monitoring real-time data, manufacturers can detect bottlenecks, identify areas for improvement, and optimize production lines to increase efficiency.
Predictive maintenance is yet another game-changer. Digital Twins can analyze the performance data of machines, identify patterns of failure, and predict maintenance requirements. This ensures that machines are repaired or replaced before they cause any significant downtime.
Transforming the Supply Chain Industry
So, how do Digital Twins bring their magic to the supply chain industry? Improved inventory management is one major benefit. By creating a virtual replica of the entire supply chain network, companies can track inventory levels, identify shortages or excesses, and streamline procurement and distribution.
Enhanced logistics and shipping is another area where Digital Twins make an impact. By analyzing data from transportation vehicles, companies can optimize routes, reduce fuel consumption, and improve delivery times.
Demand forecasting is yet another area where Digital Twins prove their worth. By analyzing historical sales data, market trends, and other factors, companies can accurately predict future demand and plan their inventory accordingly, reducing stockouts and excess inventory.
Challenges and Future Implications
Digital twins are revolutionizing the manufacturing and supply chain industry, but there are challenges to consider. Privacy and security concerns arise from the collection of massive amounts of data, as unauthorized access or breaches could have disastrous consequences. Integrating digital twin technology into existing systems is also a complex process with compatibility issues and technical barriers. However, the future potential of digital twins is vast. Optimized manufacturing processes, predictive maintenance, and efficient supply chain management are just the beginning. While challenges exist, overcoming them can lead to a revolution in the industry. Strap in for a wild ride into the future where digital twins take the lead, bringing wonders and innovations we can only imagine.
Conclusion
Digital twins are revolutionizing the manufacturing and supply chain industry by replicating physical assets and processes in a digital environment. They offer benefits such as improved product design, optimized production processes, predictive maintenance, enhanced inventory management, optimized logistics and shipping, and accurate demand forecasting. However, challenges like privacy and security concerns, as well as integration issues, need to be addressed. Despite these challenges, the future of digital twins looks promising, with endless possibilities for innovation and improvement in manufacturing and supply chain operations.
Share this post