In any production plant, operations, quality, and maintenance teams face constant challenges. Efficiency losses, unexpected stops, quality problems… Every day brings with it new questions that need quick and accurate answers.
However, many times the difference between a company with highly optimized processes and one with constant problems lies not in technology or resources, but in something much more basic: the ability to ask the right question and find the answer in the data.
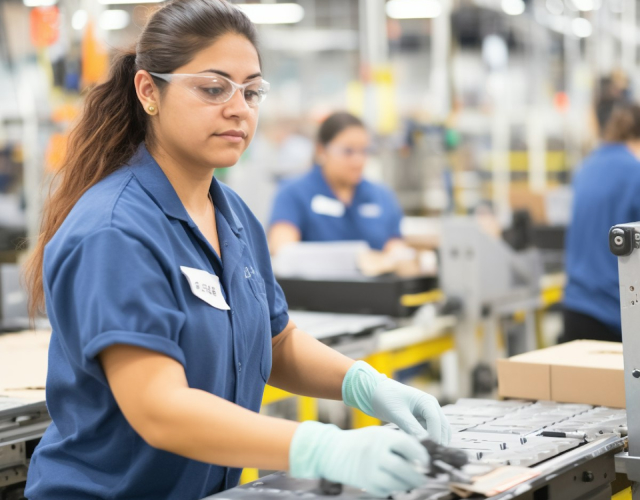
What is affecting the efficiency of my production?
This question may seem simple, but in many companies it is still difficult to answer accurately. Often, problems in production are detected too late, when costs have already skyrocketed or production has already suffered irreparable delays.
The main causes of this lack of visibility are usually:
- Fragmented data: Information is scattered across systems, spreadsheets, or manual reports, making it difficult to see the big picture.
- Reactive instead of proactive analysis: Instead of anticipating problems, many companies only act when failures have already occurred.
- Lack of correlation between data and real causes: Having data doesn’t always mean understanding it. Without the right tools, it is difficult to identify patterns and detect the true causes of problems.
The challenge: transforming questions into strategic decisions
To optimize processes effectively, it’s critical to change the way data is analyzed and decisions are made.
Instead of asking themselves in a general way “Why is my production inefficient?”, the most competitive companies ask strategic questions based on concrete data:
- What is the main cause of my downtime?
- How does variability in raw materials affect product quality?
- Where is the greatest waste being generated in the production line?
- What is the real impact of changes in machinery configuration?
Answering these questions requires more than intuition or experience. It requires actionable data, in real time and with tools that facilitate its interpretation.
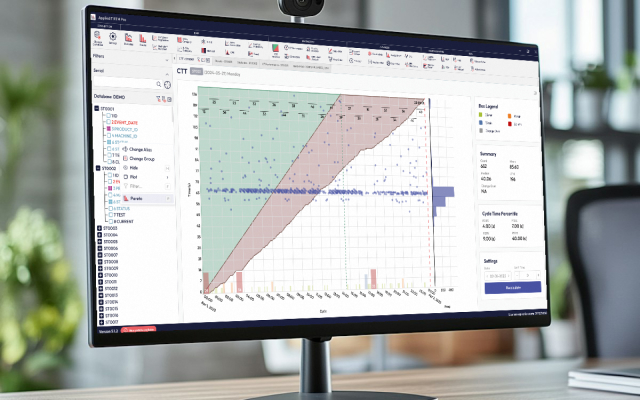
The Solution: Smart Questions Backed by RTM Pro
This is where a tool like RTM Pro makes a difference. It’s not just about collecting data, it’s about turning it into useful information for decision-making.
With RTM Pro, you can:
- Monitor in real time the performance of each process and production equipment.
- Identify patterns and trends to anticipate potential failures or inefficiencies.
- Automate reports and alerts to make faster, data-driven decisions.
- Optimize plant performance by adjusting parameters based on accurate information.
Practical example
Imagine that your plant has experienced an increase in the number of defective products in the last week. Without an advanced tool, it could take days to analyze the logs and find the cause.
With RTM Pro, in a matter of minutes you could detect that:
- The problem started after a change in a machine’s settings.
- Variability in operating temperature is affecting product quality.
- Operators have not received real-time alerts, so the problem has persisted.
With this clear and accessible information, you can act immediately, prevent losses and improve quality without waiting for the problem to worsen.
Conclusion: Asking is the first step, analyzing is the way, acting is the key
Continuous improvement doesn’t happen by accident. It starts with the curiosity to understand what can be improved, is strengthened with tools that provide data-based answers, and is concretized with well-informed strategic decisions.
If you want to take your production to another level, the question isn’t whether you should optimize your processes, but when you’re going to start.
Request a demo of RTM Pro and find out how you can transform simple questions into real improvements.
Share this post