In the world of manufacturing, operational efficiency does not start when the machines are up and running, but long before. At AppliediT, we have developed the concept of (Pre)Ramp-up, a proactive methodology that allows us to anticipate production challenges even before stations are fully built.
This approach, designed to analyse Overall Equipment Efficiency (OEE) potential at the end of the design phase, is changing the rules of the game by ensuring that projects get off to an optimal start, with risks controlled and efforts focused on what really matters.
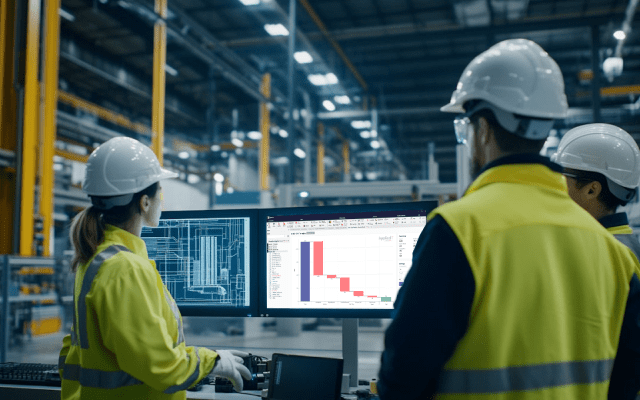
What is (Pre)Ramp-up and why is it innovative?
The (Pre)Ramp-up is much more than a simple evaluation; it is a strategic tool that takes advantage of the critical moment when the stations of the production line are still being developed by the machine supplier.
This process includes:
- Assessment of the OEE potential of each station in the line, identifying possible bottlenecks and constraints.
- Simulation of the OEE of the entire line, based on actual design and construction data.
- Identification of key risks that could impact future performance, prioritising the most relevant actions.
Rather than providing long lists of tasks that overwhelm teams, the (Pre)Ramp-up generates a focused set of high-priority actions. This approach ensures that resources are strategically directed to what will have the greatest impact on final performance.
Tangible benefits of (Pre)Ramp-up
Implementing this methodology can make the difference between a bumpy production start-up and a smooth and efficient ramp-up. Some of the most notable benefits include:
- Improved Risk Management: Identified and mitigated bottlenecks before line setup.
- Optimized Performance: Delivered an actionable plan to achieve OEE targets faster.
- Time Savings: Reduced ramp-up duration by 20% through better preparation.
- Cost Avoidance: Avoided penalties from underperformance during initial production.
- Customer Confidence: Gained stakeholder trust with a clear, focused plan and simulation-based predictions.
Case study: success with (Pre)Ramp-up
In one of our recent projects, we collaborated with a customer who was in the final design phase of a critical production line. Through (Pre)Ramp-up, we detected that three specific stations had a significantly lower OEE potential than projected, due to restrictions in their synchronisation capacity.
Thanks to this early assessment:
- Design parameters were adjusted before the stations were assembled.
- The configuration of the affected stations was optimised, increasing their OEE potential by 15%.
- The project was able to start operations at close to 95% of its projected capacity from day one, avoiding delays and cost overruns.
This is just one example of how our methodology transforms challenges into opportunities and ensures outstanding results.
Why choose AppliediT as your (Pre)Ramp-up partner?
At AppliediT, we don’t just implement innovative methodologies; we are pioneers in creating solutions that make a real difference to our clients’ efficiency and competitiveness.
(Pre)Ramp-up is one of our most effective approaches to accompany you on the road to operational excellence, aligning design objectives with expected performance and ensuring that every project starts off on the right foot.
Want to transform your next project?
Contact our experts and find out how (Pre)Ramp-up can help you maximise performance right from the design phase – let’s talk about how to take your production line to the next level!
Share this post